Wearable Tags vs Shuttle Sensors: Which Safety System Works Best?

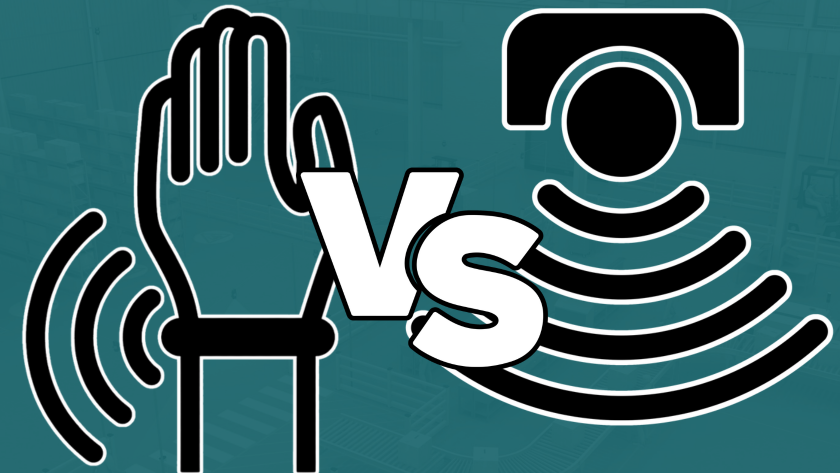
When it comes to workplace safety, businesses need reliable and cost-effective solutions to prevent accidents. Two of the most discussed options today are wearable proximity tags and shuttle sensors: both are designed to reduce the risk of collisions between pedestrians and moving vehicles.
But which system delivers the best results? In this article, we’ll compare the pros, cons, and costs of each, helping you decide which is right for your business.
Wearable Proximity Tags: Pros & Cons
Wearable tags are small electronic devices worn by workers that interact with site-wide sensors to detect potential collisions. If a pedestrian enters a restricted area or moves too close to a vehicle, an alarm is triggered to warn both the worker and the operator.
The Pros
✅ Real-time alerts – Instantly warns both workers and drivers when a hazard zone is breached.
✅ Versatile tracking – Can be attached to personnel, equipment, or vehicles for wider coverage.
✅ Data insights – Logs near-miss incidents, allowing businesses to refine safety protocols over time.
The Cons
❌ Workers must wear the tags – If forgotten, lost, or removed, the system is useless.
❌ Battery & maintenance issues – Tags require regular charging or battery replacement.
❌ False alarms – Sensitivity settings can trigger unnecessary alerts, which can lead to workers ignoring warnings over time.
❌ Higher long-term costs – A typical, basic forklift tag system costs around £3,500+, with additional ongoing costs for tag replacements, maintenance, and training.
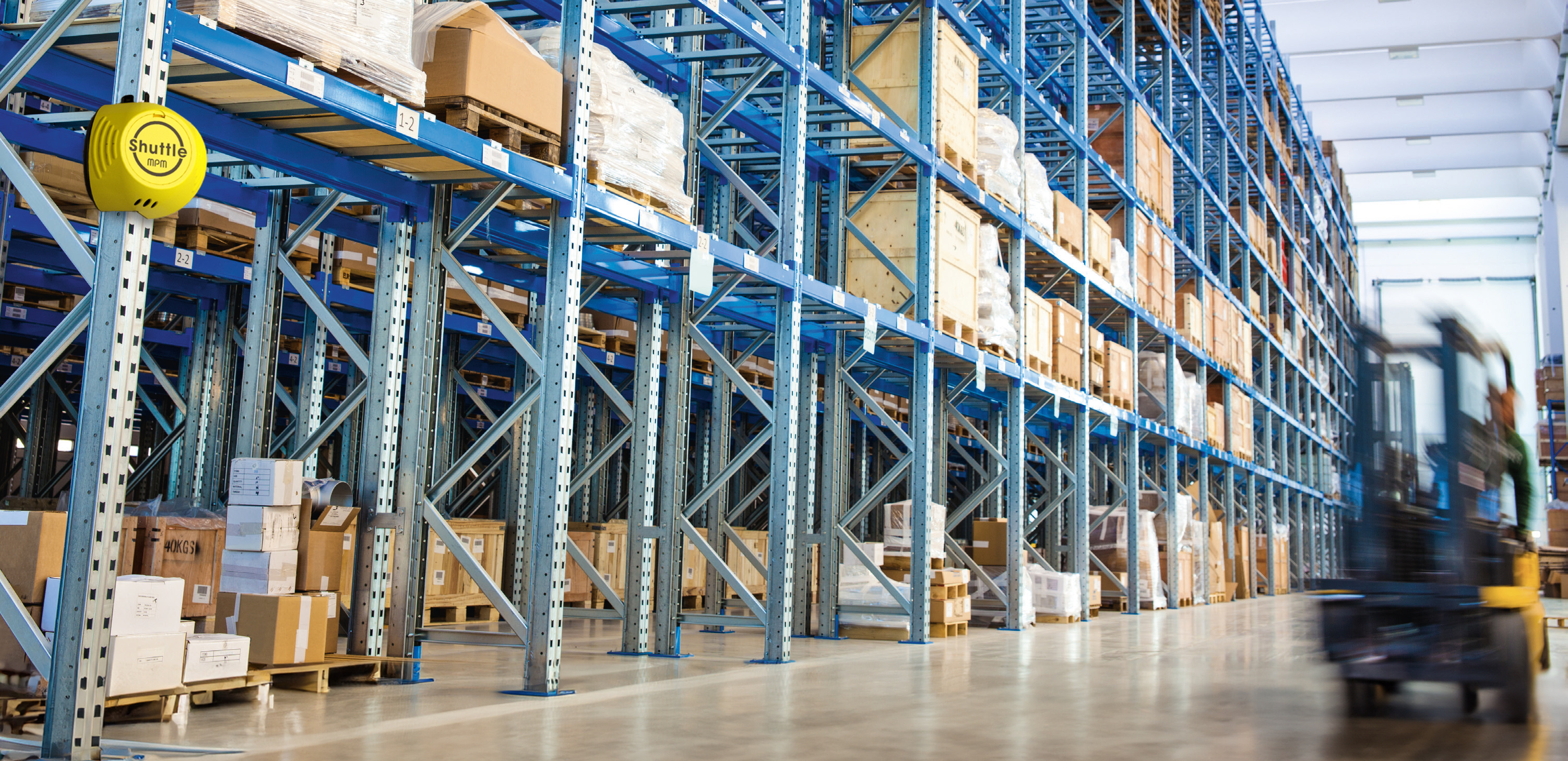
Shuttle Sensors: A Smarter, Passive Solution?
Unlike wearable tags, shuttle sensors are installed in high-risk areas and automatically detect movement without needing workers to wear devices. These systems use audio and visual alerts to warn both pedestrians and vehicle operators when a potential collision is detected, particularly in blind spots and busy intersections.
The Pros
✅ Always active – No reliance on workers remembering to wear a device, ensuring continuous protection.
✅ Detects all movement – Identifies pedestrians, forklifts, and other vehicles without requiring individual tags.
✅ Minimal maintenance – Once installed, the system operates automatically with little upkeep.
✅ Significantly lower cost – A shuttle sensor costs less than £400, making it a budget-friendly alternative to tag-based systems.
The Cons
❌ Limited to fixed locations – Shuttle sensors are ideal for warehouses and factories, but they don’t track movement across an entire site like wearable tags.
❌ May not work well outdoors – In open spaces with strong sunlight or adverse weather, sensor accuracy may be affected.
Cost Comparison: Which System is Right for You?
While both solutions enhance workplace safety, the cost structure varies significantly:
- Wearable Tags: A basic forklift tag system can cost over £3,500, plus ongoing expenses for lost/damaged tags, battery replacements, and training. Over time, businesses may spend significantly more maintaining and managing the system.
- Shuttle Sensors: Costing under £400, shuttle sensors provide a lower-cost, low-maintenance alternative with no ongoing wearables or replacements required.
Ultimately, the right choice depends on your specific needs. Wearable tags provide full tracking and alerts across a large site, while shuttle sensors offer a simple, cost-effective safety solution for high-risk areas.
At Clarity, we offer both solutions and can help you choose the best system for your site. Whether you need wearable tag systems or advanced shuttle sensors, we can help you find the right fit for your site.
Get in touch today to explore the best safety technology for your workplace.